CÓMO PREVENIR LA CORROSIÓN EN BOMBAS: LA GUÍA COMPLETA
Al momento de tomar una decisión de selección o compra de una bomba, muchas veces se desconoce la compatibilidad química del fluido que necesitan bombear y no es hasta que el equipo se daña prematuramente (impulsores, sello mecánico, etcétera) que se cuestiona si el material de construcción del sistema de bombeo es el adecuado para su aplicación.
En esta guía revisaremos los aspectos clave que participan en el proceso de corrosión de un equipo y cómo podemos seleccionar un material de construcción de acuerdo con el perfil químico de la sustancia a bombear.
1. ¿QUÉ ES LA CORROSIÓN Y CÓMO AFECTA A SU SISTEMA?
La corrosión es el resultado de una reacción electroquímica (oxido-reducción) entre dos materiales, o bien, un material y su entorno, dando lugar a un deterioro en el mismo. La corrosión es provocada debido al flujo masivo de electrones generado por las diferencias químicas de las sustancias. Esta corriente de electrones se establece cuando existe algo llamado diferencia de potenciales. Existen dos participantes en este intercambio de electrones, se dice que la sustancia que los emite (o cede) se comporta como un ánodo y se oxida, y aquella que los recibe se comporta como un cátodo y en ella se verifica la reducción.
En la industria del bombeo, la corrosión es un grave problema; puede provocar averías, tiempos muertos, accidentes y, a su vez, pérdidas millonarias. Hay muchas formas de prevenir o abordar este problema, la mejor es conocer si el material del equipo es apto para las condiciones del lugar o sitio donde va a estar instalado.
2. ¿CÓMO DETERMINAR LA ALCALINIDAD O ACIDEZ DE UNA SUSTANCIA A TRAVÉS DEL PH?
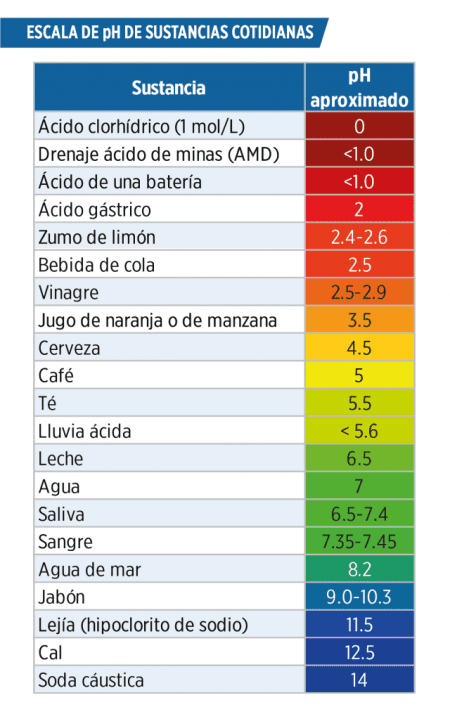
El Potencial de Hidrogeno, o bien, el pH, es una medida que se usa para determinar la acidez o alcalinidad de las sustancias y este a su vez indica la concentración de iones de hidrogeno presentes en las mismas. En esta escala es posible encontrar valores desde 0 (ácido) hasta 14 (alcalino), siendo 7 el punto medio para representar la neutralidad. Por ejemplo, el agua fresca tiene un PH de 7. Mientras las sustancias se ubiquen más a los extremos de esta escala, hay mayor riesgo de tener un intercambio de electrones por el diferencial de potenciales entre el material de la bomba y el líquido transferido, dando a lugar a un deterioro en los materiales de la bomba, es decir, corrosión.
Como se mencionó anteriormente, la temperatura juega un papel muy importante en la velocidad que se produce la corrosión. Mientras más caliente sea el líquido que se bombea, incrementará la velocidad en la que la reacción química es producida.
3. ¿CUÁLES SON LOS MATERIALES COMUNES DE CONSTRUCCIÓN DE BOMBAS POR APLICACIÓN?
Existen muchas opciones disponibles: desde el uso de hierro, aceros inoxidables, termoplásticos hasta aleaciones especiales.
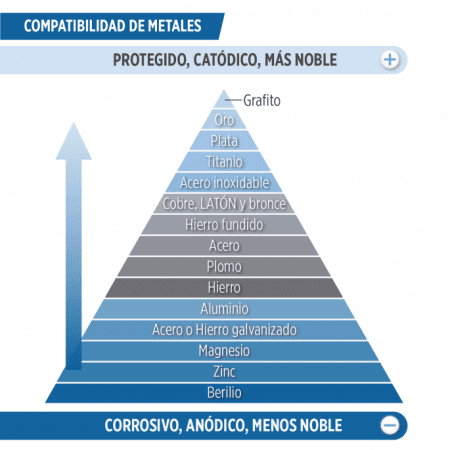
El material mayormente utilizado para las bombas de agua centrifugas es el hierro fundido; el simple contacto con ambientes húmedos produce oxido, sin embargo, en sistemas de agua potable este material no presenta un desgaste o daño significativo siendo que el PH es igual a 7 (Neutro) y la temperatura no suele ascender a los 25°C.
En perforaciones o agua subterránea es posible tener una mayor cantidad de cloruros (sales) y minerales que pueden alterar el PH del agua; tal es el caso de pozos de agua en zonas costeras donde, por experiencia, los usuarios conocen que se requiere un material de construcción distinto al hierro, para conseguir mayor durabilidad del equipo. Dependiendo de la concentración de solutos, el material óptimo para estas aplicaciones es el acero inoxidable 316 o inclusive el grado 904L.
Anodos de Sacrificio
Una alternativa menos costosa para prolongar la vida de los equipos que están expuestos a ambientes corrosivos es el uso de ánodos de sacrificio. Esta opción permite al usuario usar un sistema de bombeo con un grado menor de acero inoxidable, es decir 304 en vez de 316, lo cual es menos costoso en la adquisición de los equipos. Este accesorio, como su nombre indica, es para sacrificio en la reacción oxido-reducción, es decir, es el material que estaría cediendo electrones y se oxidaría primero antes que el motor y la bomba, prolongando la vida y uso del sistema de bombeo. Para que este accesorio funcione adecuadamente tiene que estar en contacto directo con el sistema de bombeo. Para sistemas de bombeo sumergibles de 4” el kit de Ánodo de Sacrificio de Franklin Electric se puede utilizar para prevenir la una falla prematura del motor en aplicaciones sumamente corrosivas.
En el portafolio de soluciones de Franklin Electric hay bombas sumergibles troqueladas en SS316 como la bomba Serie SR, y una línea para ambientes más agresivos y de alto caudal como lo es la Serie FS, en fundición SS316. La Serie VR es ideal para aplicaciones industriales que demanden el uso de materiales resistentes para el bombeo, gracias a su construcción en SS316 permite también trabajar en temperaturas extremas y además están certificadas bajo la norma NSF-61 lo que las hace aptas para su uso en sistemas de agua potable.
Otra aplicación muy común donde se usan materiales distintos a los convencionales en las bombas es en los sistemas de recirculación de agua para Spas, donde los materiales por preferencia para la construcción de los sistemas de bombeo son los termoplásticos. Muchos de los tratamientos o soluciones que son recirculados en tinas o sistemas de hidromasaje contienen altos niveles de sales y temperaturas por encima de los 25°C, por ello es necesario reemplazar el uso de metales por plásticos que no reaccionen con estas sustancias. Para estas aplicaciones, Franklin Electric ha desarrollado varias líneas de sistemas de bombeo con hidráulica en termoplásticos, tales como la Serie A y S y la Serie JCM.
4. ¿LA TUBERÍA PUEDE PROVOCAR CORROSIÓN EN EL SISTEMA DE BOMBEO?
Otro aspecto muy importante que se debe tener en cuenta son los materiales para la red de suministro de agua. Si los accesorios y tuberías son de metales distintos a la bomba, hay que tomar en cuenta su compatibilidad. Por ejemplo, si usamos una bomba en acero inoxidable con tubería de hierro galvanizada es muy probable que veamos oxidación en los puntos de contacto de los materiales. Este tipo de reacción puede que no sea critica directamente sobre nuestra bomba, pero puede provocar taponaduras y reducción de los diámetros a la succión y descarga, causando otro tipo de problemas como la cavitación.
Aunque existen infinidad de aplicaciones donde las bombas pueden ser expuestas o sometidas a ambientes corrosivos, que difícilmente pueden ser abarcadas en su totalidad, esperamos que este artículo sirva como guía para que usted pueda tomar una decisión más acertada al seleccionar un equipo y prolongar así la vida útil de su inversión. Para más información y solución de dudas sobre su aplicación contacte a un representante de Franklin Electric, a su gerente de territorio o Ingeniero de servicio.
Por: Ramiro Vigil Rangel
Sobre el Autor
Ramiro Vigil Rangel es Senior Product Manager para Franklin Electric Latinoamérica. Calificado profesionalmente en Ingeniería Mecatrónica, Ramiro aporta su amplia experiencia en materia de Automatización, Instrumentación y Sistemas de Bombeo, además de que anteriormente se desempeñaba como Ingeniero de Aplicaciones con especialidad en los segmentos de HVAC y Construcción para nuestra compañía y previamente, como Ingeniero Campo en la Evaluación de Reservorios para Halliburton en la Industria Petrolera.
Si deseas conocer más acerca de estos productos contáctate con tu asesor de Acero Comercial Ecuatoriano o escribanos a los siguientes correos:
-
Regiones Sierra y Oriente: infouio@acerocomercial.com
-
Región Costa e Insular: infogye@acerocomercial.com
No olvides suscribirte a nuestras redes sociales para que estés al tanto de todos nuestros eventos, promociones, productos y capacitaciones.